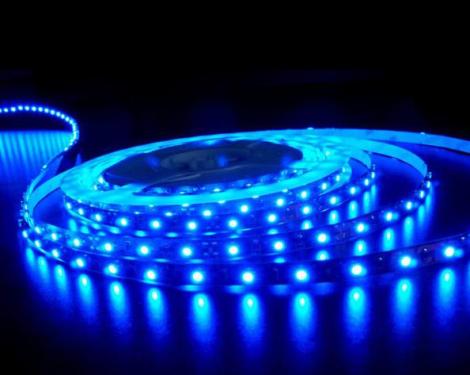
In the case of high-power LED packaged products, the use of heat-dissipation countermeasures is very troublesome. In this context, it is highly cost-effective, and the product development trend is similar to metal-based substrates and other high-heat-dissipating package substrates, resulting in higher LED efficiency. One of the most popular spots.
1. High-efficiency Metal Substrate Concerns Hard metal-based package substrates utilize conventional resin substrates or ceramic substrates to impart high thermal conductivity, processability, electromagnetic wave shielding, thermal shock resistance, and other metal properties to form new generations. Power LED package substrate.
The high-power LED package substrate is made of an epoxy resin adhesive, and the copper foil is adhered to the surface of the metal substrate. The combination of the metal substrate and the material of the insulating layer changes the LED package substrate into various applications.
High heat dissipation is an essential characteristic of a substrate for high power LED packages. Therefore, materials such as aluminum and copper are used for the above-described metal-based LED package substrates, and an epoxy resin having a highly thermally conductive inorganic filler (Filler) is often used for the insulation layer. The aluminum substrate is made of high thermal conductivity and light weight aluminum using high density packaging substrate, has been applied in air conditioners converter (Inverter), communications equipment, power supply substrate and other fields, also applies to high power LED package .
In general, the equivalent thermal conductivity standard of a metal package substrate is about 2 W/mK. To meet the high power requirement of 4 to 6 W/mK for a customer, the industry has introduced a metal-based package substrate that is equivalent and has a thermal conductivity of more than 8 W/mK. . Since the main purpose of the hard metal-based package substrate is to support high-power LED packages, each package substrate manufacturer is actively developing technologies that can improve thermal conductivity.
The main feature of a hard metal-based package substrate is high heat dissipation. High thermal conductivity insulating layer package substrate can greatly reduce the temperature of the LED chip. In addition, the heat dissipation design of the substrate, through the combination of the heat dissipation film and the package substrate, is also expected to extend the service life of the LED chip.
The disadvantage of the metal-based package substrate is that the thermal expansion coefficient of the metal of the substrate is very large, which is similar to the situation when the ceramic chip component with a low thermal expansion coefficient is soldered, and is susceptible to thermal cycling. If a high-power LED package uses aluminum nitride, the metal-based package substrate Uncoordinated problems may occur, so it is necessary to absorb the thermal stress caused by the difference in thermal expansion coefficient of each material of the LED module, thereby relaxing the thermal stress and improving the reliability of the package substrate.
2. Package substrate manufacturers actively develop flexible substrates The main applications of flexible substrates are mostly focused on wiring substrates. In the past, high-efficiency devices such as high-power transistors and ICs have hardly used flexible substrates. In recent years, liquid crystal displays have been satisfied. High-brightness demand strongly demands that the flexible substrate can set high-power LEDs at a high density. However, the heat generated by the LED causes the service life of the LED to decrease. However, it becomes a very difficult technical task. Although the use of an aluminum plate can enhance the heat dissipation performance, However, there are cost and assembly restrictions that cannot be solved fundamentally.
The highly heat-conducting flexure substrate is adhered to the insulating layer with a metal foil. Although the basic structure is the same as that of the conventional flexure substrate, the insulating layer is filled with a soft epoxy resin and filled with a highly thermally conductive inorganic filler, and has a hard metal system. The thermal conductivity of the package substrate is 8W/mK at the same level, and it is also flexible, flexible, highly heat conductive, and highly reliable. In addition, the flexible substrate can also be designed according to customer needs, single-sided single-layer panel single-sided double-layer, double-sided double-layer structure.
The main feature of a highly heat-conducting flexible substrate is that high heat-generating elements can be provided and assembled three-dimensionally, that is, free bending characteristics can be achieved, and high assembly space utilization can be obtained.
According to the experimental results, the temperature of the LED is reduced by about 100C when a substrate with high thermal conductivity is used, which means that the decrease in the service life of the LED can be expected to be improved. In fact, in addition to high-power LEDs, other high-power semiconductor devices can be provided on high-heat-flexible substrates, which are suitable for applications such as space-constrained or high-density packaging, which require high heat dissipation.
With regard to the heat dissipation characteristics of similar LED modules used for illumination, the package substrate alone cannot meet actual needs. Therefore, the mating of the peripheral materials of the substrate becomes very important. For example, with the 3W/mK thermal conductive film, the heat dissipation of the LED module can be effectively improved. And assembly workability.
3. The ceramic package substrate is very advantageous for thermal skew. As described above, the heat generation of the white LED continues to rise as the input power intensity increases, and the temperature rise of the LED chip causes the light output to decrease. Therefore, the review of the LED package structure and used materials is very important. In the past, LEDs were packaged using a low thermal conductivity resin and were considered as one of the factors that affect the heat dissipation characteristics. Therefore, in recent years, high-thermal-conductivity ceramics or resin-packaged structures with metal plates have been gradually adopted. The commonly used methods for high-power LED chips include: large-sized LED chips, improved LED chip light-emitting efficiency, high light extraction efficiency, and high current.
Although the increase in the amount of current emission will increase in proportion, the heat output of the LED chip will also increase. Because the irradiance saturation and attenuation appear in the high-input area, this phenomenon is mainly caused by the LED chip heating. Therefore, when the LED chip is high-powered, it must first solve the heat dissipation problem.
The LED package not only protects the internal LED chip, but also functions as an LED chip and the outside for electrical connection and heat dissipation. The LED package requires that the light generated by the LED chip can be efficiently extracted to the outside. Therefore, the package must have high strength, high insulation, high thermal conductivity and high reflectivity. Surprisingly, ceramics have almost all of the above characteristics, and the ceramic is resistant to Heat and light deterioration are also superior to resins.
4. The traditional high heat dissipation package is to place the LED chip on the substrate and cover the resin around the substrate. However, the metal thermal expansion coefficient of the package method is quite different from that of the LED chip. When the temperature change is very large or the package operation is not proper Heat deflection can easily occur, which can cause chip defects or reduce the efficiency of light emission.
In the future, when large-scale development of LED chips is faced, the thermal skew problem will inevitably become a problem that cannot be ignored. For these problems, ceramics having a coefficient of thermal expansion close to that of the LED chips can be said to be very favorable materials for thermal skewing measures.
In order to improve the heat transfer characteristics of the LED's high-heat emission to the outside, many cooling fans and heat exchangers have been used in the past. Actual heat dissipation is not required for consumers and lighting fixture manufacturers due to noise and space limitations. The components, which means that the non-forced heat dissipation design must greatly increase the area of ​​the frame and the external contact, and at the same time improve the heat dissipation of the package substrate and the housing.
Specific countermeasures such as: the use of far-infrared heat radiation to promote the thermal radiation of the copper layer surface heat deflection film, etc., according to experimental results confirmed the use of the heat dissipation effect of the heat dissipation film heat dissipation, almost the same area cooling film cooling fan If the flexing heat sink film is attached to the package substrate or the frame body, or the smear layer is directly applied to the package substrate or the frame body, the heat dissipation can theoretically be improved.
The packaging structure of high-power LEDs requires micro-wiring technology that can support epitaxial junctions of LED chips. Regarding the development of materials, although aluminum nitride has been highly thermally conductive, the interaction between high thermal conductivity and reflectivity has become another thorny issue. It is generally believed that if the thermal conductivity of aluminum nitride can be improved in the future, it will be beneficial to high-power LED packaging materials.
Porcelain insulation
Porcelain Insulator is made of ceramic materials. The surface of porcelain is usually covered with enamel to improve its mechanical strength, waterproof and wet, and increase the surface smoothness. The combination of porcelain and other minerals allows current to pass without reacting with nearby electrical conductors. Ensuring greater safety, High Voltage Porcelain Insulators also allows current to pass without losing any power. There are several types ofHigh Voltage Porcelain Insulators and low volatage porcelain insulators : Switch Post Insulators, Din Insulators , Line Post Insulator , Station Post Insulator, Disc Insulator , Pin Insulator , Long Rod Insulator , Porcelain Bushing , Strain Insulator , spool insulator, Shackle Insulator and Telephone Line Insulator.
Porcelain insulators are used for high-voltage and low-voltage transmission lines and dielectrics produced by various electrical equipment to support and suspend overhead conductors to maintain sufficient insulation between conductors and conductors and between conductors and the earth. The installation height should be below 1000 meters. The voltage can reach 0.3kv-330kv. They have a higher leakage distance distribution and stronger compression.
We warmly welcome friends both domestic and abroad to visit our company, if you have any questions, please contact with us directly.
Porcelain Insulator
Porcelain Insulator ,High Voltage Porcelain Insulators,Switch Post Insulators,Din Insulators
FUZHOU SINGREE IMP.& EXP.CO.,LTD. , https://www.cninsulators.com