I would like to say a few words to friends who are using the power supply potting glue, especially those who are choosing the potting glue.
First, why the glue and glue requirements: This is simple to say, it may be that the customer requires glue, it may be that others are looking for glue in the glue. To be sure, there are several major purposes and requirements for potting:
1. Waterproof, potting glue encapsulates the electrical part of the whole product tightly and completely isolated from the outside world; what water, moisture, acid and alkali salts can not meet the circuit components, can improve the waterproof, moisture and corrosion resistance. Therefore, the glue you choose should have good fluidity. If the fluidity is not good, how can it be deeply penetrated and completely sealed? Then the adhesive force should be provided. Otherwise, the hot and cold alternately after the potting is separated from the components, the product life is not used. Performance is also affected.
2, thermal conductivity, power supply is a power product, is the conversion, control, outward output energy. Product work must be hot, such as switch tubes, transformers, electrolytic capacitors, inductors, etc. which are not heat-emitting devices and are afraid of heat devices. What to do, we must send it out as quickly and as much as possible. Therefore, the glue definitely requires good thermal conductivity. It can be said that the higher the thermal conductivity of the rubber, the better. Electrolytic capacitors in the power supply, the temperature is about half of the temperature rise for every ten degrees, but you can't add heat sinks to it; transformers, inductors, temperature, and high parameters are all difficult to change the design. You can't add it to him. Heat sink.
The waterproof power supply needs to be sealed as a whole, and the thermal conductivity of the air is very low, mainly by convection and radiation. But convection is impossible, and the components are stuffy in the box.
Therefore, filling a good thermal conductivity adhesive can put each component on the outside to dissipate heat, which not only improves the life but also simplifies the design.
3, insulation strength, this is easy to handle. Basically all of the glue is not electrically conductive, but it should be noted that the curing reaction of the AB glue like epoxy may not be partially conductive. Also, in order to save sand in it, it is hard to say. First, is your sand processed such as dehydration treatment, or is it that your sand will interfere with curing by other elements; whether the ratio of the AB agent is reasonable, whether the mixture is sufficiently uniform, and whether other conditions are available.
4, environmental requirements, generally have been certified. It depends on whether the products offered are consistent with the certification. The price difference between environmentally friendly and non-environmental materials is still quite a lot.
5, flame retardant requirements, generally look at the flame retardant test in UL. Generally, it is required to be 94-V0 or more.
6, the other parameters are much more, you have to fill it yourself. The main thing is that your supplier should be constant, his supply should be stable, and the process should be stable. Otherwise the dispersion is too large.
Second, a little about the several kinds of glue:
1. Epoxy resin: I think it is not suitable for potting the power supply, mainly because of large shrinkage stress and poor thermal conductivity. It may strain components, pads, or change the air gap. In addition, if the curing is not complete, it may be locally conductive. Poor thermal conductivity is like putting a piece of quilt on the component and stuffing it inside. Practice has proved that the defect rate after filling is high, and the more the power supply is broken.
2, organic silica gel, a lot of used. Good thermal conductivity, water resistance, etc. are good, and the flexible potting glue will not strain the components. It is only very expensive and because it is very expensive, it is important that the products supplied are consistent with the testing and certification.
3, polyurethane, this piece is not familiar with and dare not rumor. But I heard that toxic is yet to be verified.
4, hot melt vinyl, this category of rubber is a petrochemical substrate. Solid state at room temperature, potting is heated to 130-160 liquefaction and directly potting, is a one-component flexible adhesive
3. Why does EMI deteriorate after switching power supply?
After the glue is poor, the dielectric constant of the glue is several times larger than that of air, which increases the coupling strength between the components, which makes a large amount of low-frequency switching noise more coupled to the outside by this increased capacitance.
The EMI deterioration after filling can be a problem that has plagued some engineers for a long time. Some experiences are shared for everyone:
The EMI degradation after filling is divided into: conduction (CS) variation and radiation (RS) variation;
1. Conduction deterioration, the rectification methods are: (1) EMI filter inductor oil immersion, package tape (to reduce the impact of glue filling); (2) common mode inductor with grooved skeleton, such as UU and OTC type Skeleton; (3) input to ground or surgical plus Y capacitor.
2, the radiation is worse, the rectification methods are: (1) the input or output line magnetic ring; (2) the ground line magnetic ring; (3) the material of the glue.
Pay special attention to the grounding of the radiator, the grounding process should be good, and the grounding is not good!
Integrity and caring is the purpose of our service. Affordable, cost-effective, carefully selected materials, quality Seiko. On-demand customization, fast delivery, considerate service, honest cooperation. We have used oil in many physical factories, the manufacturers directly connect with customers, and have many years of industry experience. More high-quality materials to create high-quality products.
We specialize in the production of terminal blocks, there are different types, PCB Terminal Block and Din Rail Terminal Block. You can go to our website to browse. More Spring Terminal is on sale, which can be customized according to your needs. If you are interested, you can consult us. If you need some Terminal Pins or other Terminal Block Accessories, you can also consult us, we support customization and wholesale.
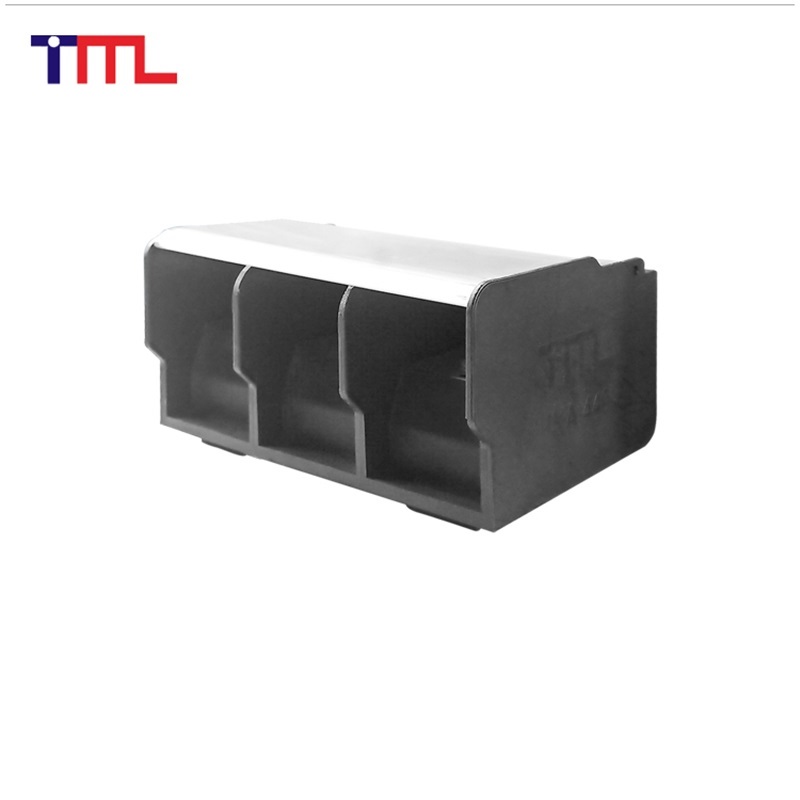
module terminal block,terminal block module,terminal block breakout module
Sichuan Xinlian electronic science and technology Company , https://www.sztmlchs.com